Wenn man sie fragt, wie sie sich Roboter vorstellen könnten, denken die meisten Menschen an große, massige Roboter, die in eingezäunten Bereichen großer Fabriken arbeiten, oder an futuristische gepanzerte Krieger, die menschliches Verhalten nachahmen.
Dazwischen zeichnet sich jedoch still und leise ein neues Phänomen ab: das Aufkommen sogenannter „Cobots“, die direkt Seite an Seite mit menschlichen Mitarbeitern arbeiten können, ohne dass Schutzzäune zu ihrer Isolierung erforderlich sind.Diese Art von Cobot kann hoffentlich die Lücke zwischen vollständig manuellen und vollautomatischen Montagelinien schließen.Bisher halten einige Unternehmen, insbesondere KMU, die Roboterautomatisierung immer noch für zu teuer und zu kompliziert und ziehen daher nie die Möglichkeit einer Anwendung in Betracht.
Herkömmliche Industrieroboter sind im Allgemeinen sperrig, arbeiten hinter Glasabschirmungen und werden häufig in der Automobilindustrie und anderen großen Montagelinien eingesetzt.Im Gegensatz dazu sind Cobots leicht, hochflexibel, mobil und können zur Lösung neuer Aufgaben umprogrammiert werden, was Unternehmen dabei hilft, sich an eine fortschrittlichere Kleinserienfertigung anzupassen, um den Herausforderungen der Kleinserienfertigung gerecht zu werden.In den USA macht die Anzahl der in der Automobilindustrie eingesetzten Roboter immer noch etwa 65 % des gesamten Marktumsatzes aus.Die American Robot Industry Association (RIA) geht unter Berufung auf Beobachterdaten davon aus, dass nur 10 % der Unternehmen, die von Robotern profitieren könnten, bisher Roboter installiert haben.
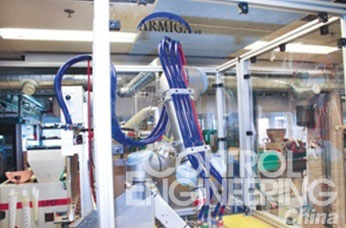
Der Hörgerätehersteller Odicon nutzt UR5-Roboterarme, um verschiedene Aufgaben in der Gießerei auszuführen, während Saugwerkzeuge durch pneumatische Klemmen ersetzt wurden, die komplexere Gussteile handhaben können.Der sechsachsige Roboter hat einen Zyklus von vier bis sieben Sekunden und kann Überroll- und Kippvorgänge ausführen, die mit herkömmlichen zwei- und dreiachsigen Odicon-Robotern nicht möglich sind.
Präzise Handhabung
Die von Audi verwendeten herkömmlichen Roboter konnten Probleme im Zusammenhang mit Anwendbarkeit und Portabilität nicht lösen.Aber mit den neuen Robotern verschwindet alles.Die Teile moderner Hörgeräte werden immer kleiner und messen oft nur noch einen Millimeter.Hörgerätehersteller haben nach einer Lösung gesucht, die kleine Teile aus Formen saugen kann.Dies ist manuell völlig unmöglich.Ebenso sind „alte“ Zwei- oder Drei-Achsen-Roboter, die sich nur horizontal und vertikal bewegen können, nicht realisierbar.Bleibt beispielsweise ein Kleinteil in einer Gussform hängen, muss der Roboter es herausklappen können.
Innerhalb nur eines Tages installierte Audicon in seiner Formwerkstatt Roboter für neue Aufgaben.Der neue Roboter kann sicher auf der Form einer Spritzgießmaschine montiert werden und saugt Kunststoffteile durch ein speziell entwickeltes Vakuumsystem an, während komplexere Formteile mit pneumatischen Spannern gehandhabt werden.Dank seines Sechs-Achsen-Designs ist der neue Roboter sehr wendig und kann Teile durch Drehen oder Kippen schnell aus der Form entnehmen.Die neuen Roboter haben einen Arbeitstakt von vier bis sieben Sekunden, abhängig von der Stückzahl und der Bauteilgröße.Aufgrund des optimierten Produktionsprozesses beträgt die Amortisationszeit nur 60 Tage.
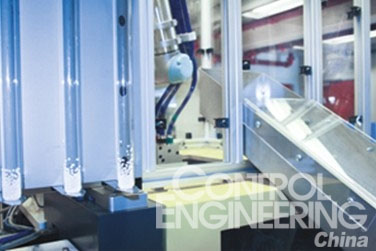
Im Audi-Werk ist der UR-Roboter fest auf einer Spritzgießmaschine montiert und kann Formen überfahren und Kunststoffteile aufnehmen.Dies geschieht mithilfe eines speziell entwickelten Vakuumsystems, um sicherzustellen, dass empfindliche Komponenten nicht beschädigt werden.
Kann auf begrenztem Raum arbeiten
Im italienischen Werk Cascina Italia kann ein kollaborativer Roboter, der an einer Verpackungslinie arbeitet, 15.000 Eier pro Stunde verarbeiten.Ausgestattet mit pneumatischen Klammern kann der Roboter den Verpackungsvorgang von 10 Eierkartons abschließen.Die Arbeit erfordert eine sehr präzise Handhabung und eine sorgfältige Platzierung, da jeder Eierkarton 9 Lagen mit je 10 Eierschalen enthält.
Zunächst hatte Cascina nicht damit gerechnet, die Roboter für die Arbeit einzusetzen, aber der Eierhersteller erkannte schnell die Vorteile des Einsatzes der Roboter, nachdem er sie in seiner eigenen Fabrik in Aktion gesehen hatte.Neunzig Tage später arbeiten die neuen Roboter am Fließband.Mit einem Gewicht von nur 11 Pfund kann der Roboter problemlos von einer Verpackungslinie zur anderen wechseln, was für Cascina von entscheidender Bedeutung ist, da das Unternehmen Eierprodukte in vier verschiedenen Größen anbietet und der Roboter auf engstem Raum neben menschlichen Mitarbeitern arbeiten muss.
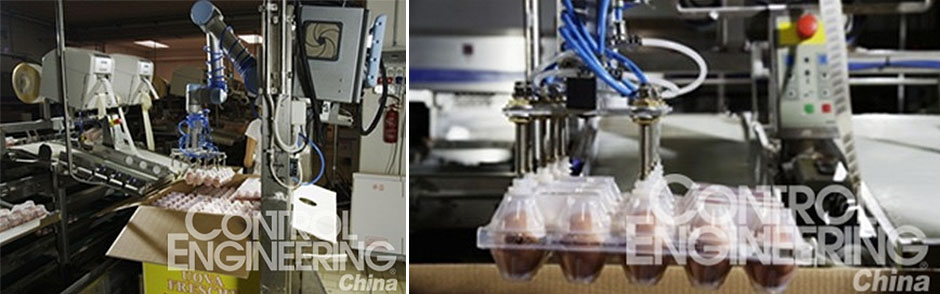
Cascina Italia verwendet den UR5-Roboter von UAO Robotics, um 15.000 Eier pro Stunde auf seiner automatisierten Verpackungslinie zu verarbeiten.Mitarbeiter des Unternehmens können den Roboter schnell umprogrammieren und ohne Sicherheitszaun neben ihm arbeiten.Da das Werk in Cascina nicht für die Unterbringung einer einzelnen Roboterautomatisierungseinheit geplant war, war ein tragbarer Roboter, der schnell zwischen Aufgaben wechseln kann, für den italienischen Eierhändler von entscheidender Bedeutung.
Sicherheit zuerst
Sicherheit war lange Zeit der Brennpunkt und die wichtigste treibende Kraft in der Forschung und Entwicklung von Roboterlaboren.Im Hinblick auf die Sicherheit bei der Arbeit mit Menschen besteht die neue Generation von Industrierobotern aus Kugelgelenken, rückwärts angetriebenen Motoren, Kraftsensoren und leichteren Materialien.
Die Roboter des Cascina-Werks erfüllen die bestehenden Sicherheitsanforderungen an Kraft- und Drehmomentgrenzen.Bei Kontakt mit menschlichen Mitarbeitern sind die Roboter mit Kraftkontrollvorrichtungen ausgestattet, die die Berührungskraft begrenzen, um Verletzungen vorzubeugen.In den meisten Anwendungen ermöglicht diese Sicherheitsfunktion nach einer Risikobewertung den Betrieb des Roboters, ohne dass ein Sicherheitsschutz erforderlich ist.
Vermeiden Sie schwere Arbeit
Bei der Scandinavian Tobacco Company können kollaborative Roboter jetzt direkt Seite an Seite mit menschlichen Mitarbeitern zusammenarbeiten, um Tabakdosen auf Tabakverpackungsgeräten zu verschließen.

Bei Scandinavian Tobacco belädt der UR5-Roboter jetzt Tabakdosen, befreit die Mitarbeiter von sich wiederholender Plackerei und versetzt sie in leichtere Jobs.Die neuen mechanischen Armprodukte des Unternehmens Youao Robot werden von allen gut angenommen.
Neue Roboter können menschliche Arbeitskräfte bei schweren, sich wiederholenden Aufgaben ersetzen und so ein oder zwei Arbeitskräfte entlasten, die diese Arbeit zuvor manuell erledigen mussten.Diese Mitarbeiter wurden nun anderen Positionen im Werk zugewiesen.Da in der Fabrik nicht genügend Platz auf der Verpackungseinheit vorhanden ist, um die Roboter zu isolieren, vereinfacht der Einsatz kollaborativer Roboter die Installation erheblich und senkt die Kosten.
Scandinavian Tobacco entwickelte ein eigenes Gerät und sorgte dafür, dass interne Techniker die Erstprogrammierung durchführten.Dies schützt das Unternehmens-Know-how, gewährleistet eine hohe Produktivität und vermeidet Produktionsausfälle sowie den Bedarf an teuren Outsourcing-Beratern im Falle eines Ausfalls einer Automatisierungslösung.Die Verwirklichung einer optimierten Produktion hat Unternehmer dazu veranlasst, die Produktion in skandinavischen Ländern mit hohen Löhnen zu belassen.Die neuen Roboter des Tabakkonzerns haben eine Investitionsrendite von 330 Tagen.
Von 45 Flaschen pro Minute bis 70 Flaschen pro Minute
Auch große Hersteller könnten von neuen Robotern profitieren.In einer Fabrik von Johnson & Johnson in Athen, Griechenland, haben kollaborative Roboter den Verpackungsprozess für Haar- und Hautpflegeprodukte deutlich optimiert.Im Rund-um-die-Uhr-Betrieb kann der Roboterarm alle 2,5 Sekunden gleichzeitig drei Produktflaschen von der Produktionslinie aufnehmen, ausrichten und in die Verpackungsmaschine legen.Die manuelle Verarbeitung kann 45 Flaschen pro Minute erreichen, verglichen mit 70 Produkten pro Minute bei der robotergestützten Produktion.
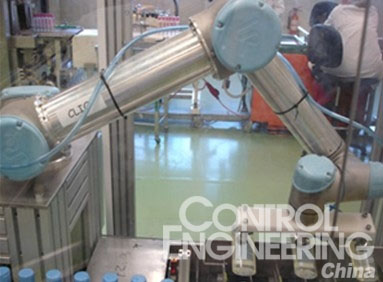
Bei Johnson & Johnson lieben die Mitarbeiter die Zusammenarbeit mit ihren neuen kollaborativen Roboterkollegen so sehr, dass sie einen Namen dafür haben.UR5 wird jetzt liebevoll „Cleo“ genannt.
Die Flaschen werden abgesaugt und sicher transportiert, ohne dass die Gefahr von Kratzern oder Verrutschen besteht.Die Geschicklichkeit des Roboters ist von entscheidender Bedeutung, da die Flaschen in allen Formen und Größen erhältlich sind und die Etiketten nicht auf der gleichen Seite aller Produkte aufgedruckt sind. Daher muss der Roboter das Produkt sowohl von der rechten als auch von der linken Seite greifen können.
Jeder J&J-Mitarbeiter kann die Roboter neu programmieren, um neue Aufgaben auszuführen, was dem Unternehmen die Kosten für die Einstellung ausgelagerter Programmierer erspart.
Eine neue Richtung in der Entwicklung der Robotik
Dies sind einige Beispiele dafür, wie eine neue Generation von Robotern erfolgreich reale Herausforderungen gemeistert hat, die herkömmliche Roboter in der Vergangenheit nicht lösen konnten.Wenn es um die Flexibilität menschlicher Zusammenarbeit und Produktion geht, müssen die Fähigkeiten traditioneller Industrieroboter auf fast allen Ebenen verbessert werden: von der festen Installation bis zum ortsveränderlichen Roboter, von sich periodisch wiederholenden Aufgaben bis hin zu häufig wechselnden Aufgaben, von intermittierenden bis hin zu kontinuierlichen Verbindungen, von keinem Menschen Von der Interaktion bis zur häufigen Zusammenarbeit mit Mitarbeitern, von der räumlichen Isolation bis zur gemeinsamen Nutzung von Räumen und von jahrelanger Rentabilität bis hin zu nahezu sofortiger Kapitalrendite.In naher Zukunft wird es viele neue Entwicklungen im aufstrebenden Bereich der Robotik geben, die die Art und Weise, wie wir arbeiten und mit Technologie interagieren, ständig verändern werden.
Scandinavian Tobacco entwickelte ein eigenes Gerät und sorgte dafür, dass interne Techniker die Erstprogrammierung durchführten.Dies schützt das Unternehmens-Know-how, gewährleistet eine hohe Produktivität und vermeidet Produktionsausfälle sowie den Bedarf an teuren Outsourcing-Beratern im Falle eines Ausfalls einer Automatisierungslösung.Die Verwirklichung einer optimierten Produktion hat Unternehmer dazu veranlasst, die Produktion in skandinavischen Ländern mit hohen Löhnen zu belassen.Die neuen Roboter des Tabakkonzerns haben eine Investitionsrendite von 330 Tagen.
Von 45 Flaschen pro Minute bis 70 Flaschen pro Minute
Auch große Hersteller könnten von neuen Robotern profitieren.In einer Fabrik von Johnson & Johnson in Athen, Griechenland, haben kollaborative Roboter den Verpackungsprozess für Haar- und Hautpflegeprodukte deutlich optimiert.Im Rund-um-die-Uhr-Betrieb kann der Roboterarm alle 2,5 Sekunden gleichzeitig drei Produktflaschen von der Produktionslinie aufnehmen, ausrichten und in der Verpackungsmaschine platzieren.Die manuelle Verarbeitung kann 45 Flaschen pro Minute erreichen, verglichen mit 70 Produkten pro Minute bei der robotergestützten Produktion.
Zeitpunkt der Veröffentlichung: 25. April 2022